AI in Fulfillment: Transforming Warehouse and Order Management by 2025
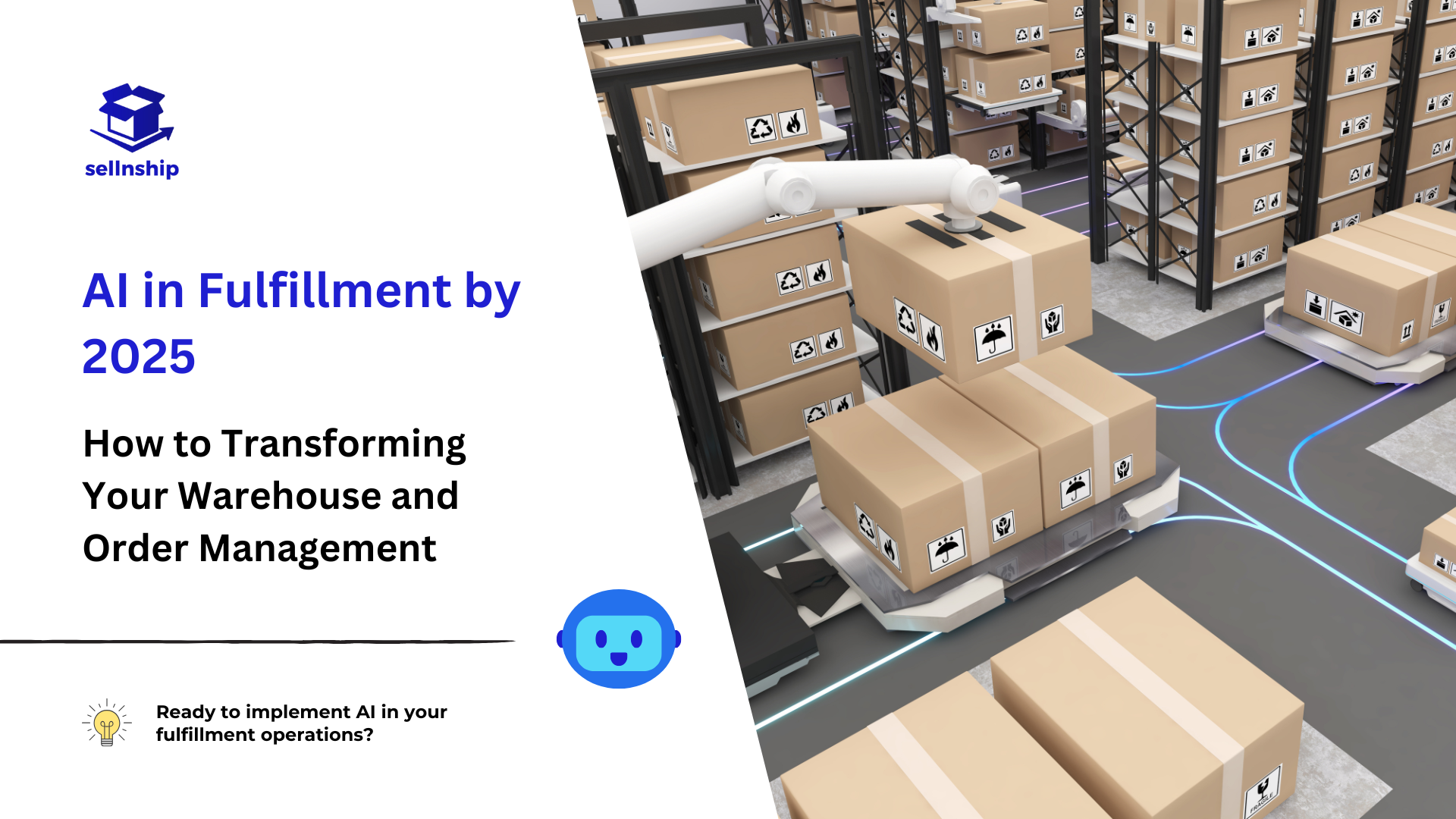
The rise of e-commerce has brought unprecedented challenges to fulfillment operations. As order volumes grow and customer expectations rise, businesses face increasing pressure to deliver faster, more accurate, and cost-efficient services. Artificial Intelligence (AI) has emerged as a game-changer in addressing these challenges, particularly in warehouse and order management.
This blog explores how AI is transforming fulfillment processes, why it’s essential for e-commerce success, and practical steps for businesses to implement AI effectively by 2025.
The Role of AI in Modern Fulfillment
AI Automates and Optimizes Operations
Artificial Intelligence has revolutionized how businesses manage their operations, especially in the fulfillment sector. AI-powered tools can automate repetitive tasks such as inventory tracking, order processing, and even packing. These tools enable businesses to streamline workflows, saving time and reducing errors.
By using AI, companies can also improve the speed of their fulfillment processes. For example, AI-driven systems can analyze historical data to predict high-demand periods, allowing businesses to prepare inventory and staffing in advance. This level of optimization is crucial for scaling operations efficiently. To see how AI is shaping logistics trends, explore our blog on AI in Logistics and Supply Chains.
Why AI Is a Game-Changer for Fulfillment
AI’s ability to process and analyze large amounts of data in real-time is unmatched. This capability helps businesses respond to challenges such as fluctuating demand or unexpected delays. For instance, AI can suggest alternative delivery routes or recommend inventory adjustments to avoid disruptions.
Furthermore, AI helps businesses achieve higher accuracy in order fulfillment. By integrating AI with Warehouse Management Systems (WMS) and Order Management Systems (OMS), businesses can ensure that every order is processed correctly and delivered on time. Learn more about sustainable applications of AI in our blog on AI-Driven Solutions for Sustainable Logistics.
Key Challenges in Fulfillment Operations
Inventory Mismanagement
Managing inventory is one of the biggest challenges in fulfillment. Businesses often face stockouts or overstocking, both of which can harm their profitability. Stockouts lead to lost sales and unhappy customers, while overstocking ties up valuable resources.
AI addresses this challenge by providing real-time inventory tracking and demand forecasting. These features enable businesses to maintain optimal stock levels, reducing the risk of disruptions while improving customer satisfaction. To stay ahead of warehousing innovations, visit our article on The 4 Warehousing Trends Experts Trust in 2024.
Order Processing Bottlenecks
Manual order processing is prone to errors and delays, especially during peak seasons. Even a small mistake can lead to incorrect shipments or missed delivery deadlines, damaging a company’s reputation.
AI-powered OMS can automate order processing tasks, ensuring that every step—from order placement to shipment—is completed seamlessly. This level of automation not only speeds up operations but also improves accuracy.
How AI Improves Fulfillment Operations
Real-Time Data and Analytics
AI systems provide businesses with real-time insights into their operations. This includes data on inventory levels, order statuses, and delivery timelines. With this information, businesses can make informed decisions to optimize their workflows.
For example, if an item is out of stock, the AI system can suggest alternatives or prioritize restocking efforts. This ensures that customers always receive timely updates and reliable service.
Smart Picking and Packing
AI-driven picking systems optimize warehouse layouts and suggest the fastest picking routes. This reduces the time workers spend locating items and ensures that orders are packed accurately. These systems can also prioritize urgent orders, ensuring they are processed first.
Additionally, AI-powered packing systems recommend the most efficient packaging solutions, minimizing material waste and lowering shipping costs. This contributes to both operational efficiency and environmental sustainability.
Conclusion
AI is transforming fulfillment by automating operations, providing real-time insights, and optimizing workflows. For businesses looking to scale and improve customer satisfaction, AI-driven tools like WMS and OMS are essential. By starting small and training your workforce, you can successfully integrate AI into your operations and achieve long-term success.
Ready to implement AI in your fulfillment operations? Contact us today to learn how SellnShip’s solutions can help your business stay ahead.